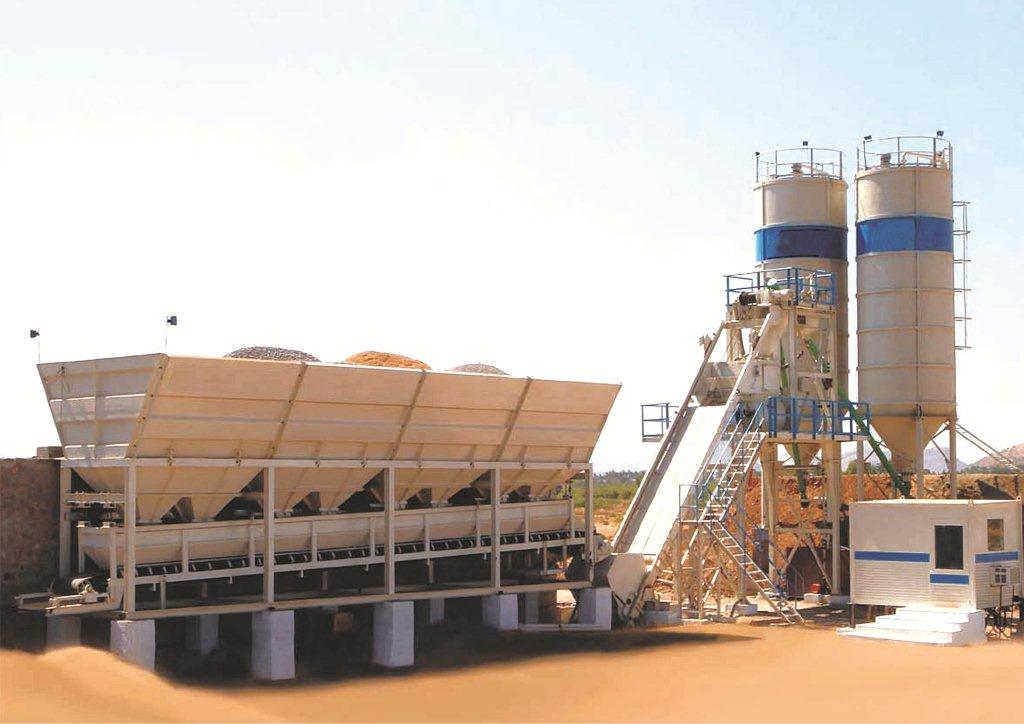
Recently, we have experienced unusually high temperatures in the United Kingdom, which spurred me to write a few lines about Concrete Batching and storage of materials.
I have tried to keep it brief, simplistic, and to the point in discussing one aspect of Hot Weather Concrete. Still, further information is already readily available elsewhere. So please send me a message if you require assistance.
The difficulties sometimes encountered during concreting in drying conditions in the United Kingdom may not be caused by frequent occurrences of these conditions but by their infrequency. Due to the humidity and cool weather, it is easy to forget the intense drying produced by heat and wind and to take no precautions against it. In many other countries, however, severe drying conditions may be the rule rather than the exception. For example, an intense sun may accompany hot, dry winds, while the wind can chill at night.
It can cause premature cracking and poor cement hydration when any influence tends to remove water from fresh or immature concrete. Any effect tends to cause an abnormal reaction rate between cement and water. If the concrete is warm, water is more likely to evaporate. A temperature rise also accelerates the reaction between cement and water. A warm concrete will therefore contain more hydration products after water is added than a cool concrete after the water has been added. This will result in a more rapid stiffening than if it were cool, apart from any workability loss caused by the mixing water’s evaporation.
The ultimate strength of the concrete will likely be noticeably lower than if it had been left cool during its early days of hardening. This is due to the greater reaction rate between cement and water in warm concrete.
Concrete properties and service life may be adversely affected when concrete is mixed, placed, and cured in hot weather.
Admixtures
Retarders depress the rate at which cement hydrates in the freshly mixed concrete and may thus usefully reduce any tendency to premature stiffening from this cause. Retarding admixtures does not eliminate the need to guard against temperature differentials in the hardening concrete.
Water-reducing admixtures are also of value in hot weather because concrete of given proportions and water content is less workable when made with warm constituents. In addition, this admixture may allow the concrete to be delivered with the intended consistency without any undesirable increase in water content.
Admixtures can neither lower the evaporative effect of drying conditions nor eliminate the potential of temperature gradients developing in the concrete forms. Effects such as these can only be minimized by appropriate mixing, transporting, placing and curing techniques.
Aggregates
Measures taken to limit the temperature of stored aggregates significantly minimise the temperature of fresh concrete . Even obstructing the sun’s rays by providing a suitable screen can result in the aggregate attaining the temperature of the air rather than the much higher temperature of aggregate exposed to the sun.
Suppose an adequate supply of water is available. In that case, it can be used to reduce still further the aggregate temperature. It should be applied to the stockpile as a fine spray rather than a jet, wetting each aggregate particle more effectively and cooling it by combined evaporation and conduction.
The shading and spraying of aggregate stockpiles are often impracticable because of their sheer size.
Nevertheless, the problems might, in many instances, be reduced to manageable proportions by limiting the amount of aggregate to be shaded and cooled to the quantity required for the next day’s concreting.
Cement
Cement stored in a silo is better protected against water vapour and carbon dioxide ingress. Still, it may absorb heat if the silo should be exposed to prolonged strong sunlight. Silos should, therefore, be protected against heat; they should be either shaded against radiation or given a coat of white or other reflective paint and, where possible, be lagged.
The use of silos implies bulk delivery of cement, and in hot weather, cement so delivered may be warmer than usual. Cement gains heat during the grinding process, but in typical weather is usually able to cool to atmospheric temperature during the stages between grinding and delivery. Hot weather slows this natural cooling process – for which there is no viable substitute, resulting that the cement may be warm when it arrives on site.
When the weather is average and mixing water and aggregates are cool, the heat contributed to the fresh concrete by warm cement is negligible. Nevertheless, in sweltering conditions, warm cement introduces a little more unwanted heat into the fresh concrete and should be avoided if possible. It is impractical to cool cement artificially before despatch. Supplies should be called forward so they may cool on site before use – mainly if spare silo capacity is available.
Water
Water taken directly from the main is likely to have a useful cooling effect because of its high specific heat and relatively low temperature.
Particularly to be avoided, if possible, is the use of warm water as the result of having been stored in tanks unprotected against heat gain.
But, on the other hand, suppose there is no alternative to storing water in tanks. In that case, these should be lagged and protected against solar radiation by shading or painting on a reflective coating.